Kun je een 3D-printer 3D-printen?
aast tijdreizen, enge buitenaardse monsters en straalgeweren is het idee van zelfreplicerende machines een terugkerend sciencefictionthema.
In 2005 begon het RepRap-project (afkorting voor “Replicating Rapid-prototyper”) met het verwezenlijken van ten minste een deel van deze sci-fi-fantasieën. Het werd gelanceerd met een ambitieuze visie: een apparaat creëren dat kopieën van zichzelf kon bouwen, “de eerste universele, zelfreplicerende productiemachine van de mensheid .”
RepRap was de katalysator voor een explosieve groei in goedkoop 3D-printen, wat leidde tot talloze innovaties en de oprichting van veel bedrijven die nu belangrijke spelers zijn in de additieve productie.
In 2007 produceerden printers die geïnspireerd waren door RepRap onderdelen om verbeterde versies van zichzelf te bouwen, op de voet gevolgd door een enorm gehypte media-aandacht voor “machines die machines maken”. Het concept van een 3D-printer die een andere 3D-printer kon printen, greep de verbeelding van het publiek aan, maar hoe dicht zijn we nu bij dat idee?
Om deze vraag te beantwoorden, nemen we een stap terug en onderzoeken we de oorsprong van RepRap, hoe het zich heeft ontwikkeld en de enorme impact die het heeft gehad op de wereld van 3D-printen en de mogelijkheden van de technologie van vandaag. We zullen onszelf zelfs toestaan om in een 3D-geprinte kristallen bol te kijken en een paar voorspellingen te doen over de toekomst.
Kun je een 3D-printer 3D-printen?
Over RepRap
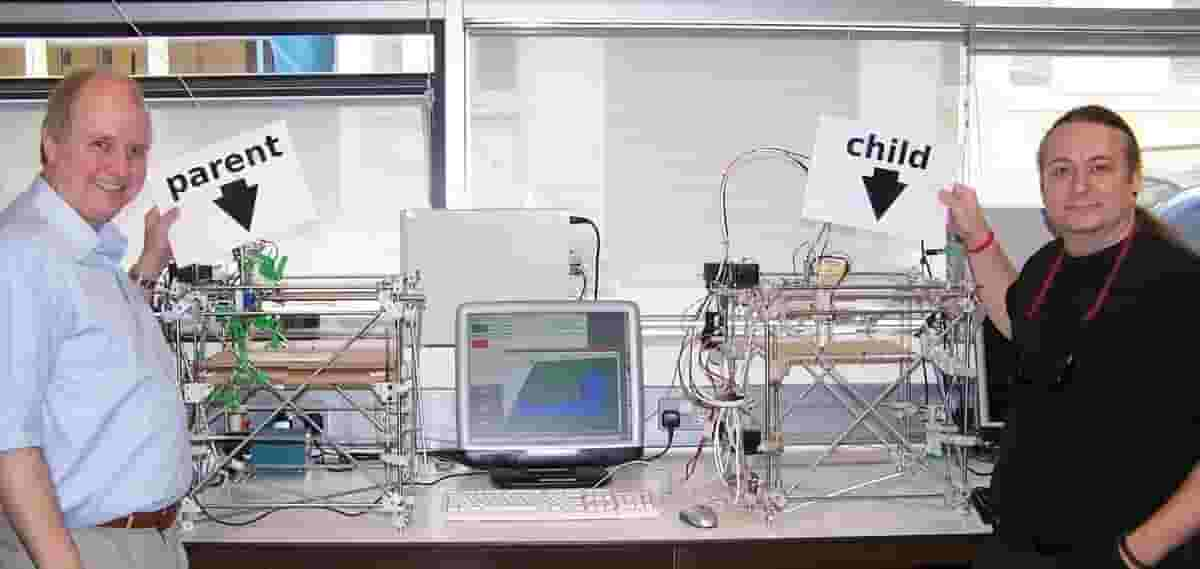
RepRap werd in 2005 gelanceerd door Dr. Adrian Bowyer , hoogleraar werktuigbouwkunde aan de universiteit van Bath in het Verenigd Koninkrijk. In die tijd gebruikten 3D-printers nog bedrijfseigen technologie en kostten ze meer dan $ 100.000. Hoewel het primaire doel was om een goedkope 3D-printer te maken die de meeste van zijn eigen componenten kon reproduceren, zag Dr. Bowyer ook een veel groter potentieel.
De uitdaging
In een reeks artikelen en conferentiepresentaties zette hij een visie uiteen van gewone mensen, met name in ontwikkelingslanden, die profiteren van de mogelijkheid om hun eigen kosteneffectieve producten te maken. Hij bracht ook alle hardware- en softwareontwerpen uit als open source, waarmee hij tientallen vrijwilligers van over de hele wereld aanmoedigde om hun expertise in te zetten. Die reis is goed gedocumenteerd in het RepRap-projectlogboek .
Na het eerste grondwerk werd in 2007 de eerste productie-3D-printer van RepRap gebouwd. Toepasselijk genoeg kreeg deze de naam ” Darwin “. Het open-sourceontwerp en de verwachte ontwikkeling ervan trokken de hulp in van tientallen projectvrijwilligers. In 2009 werd een vereenvoudigde en verbeterde RepRap-machine, ” Mendel “, gemaakt, gevolgd door ” Huxley ” in 2010.
Het aantal bijdragende projecten explodeerde tot meer dan 2.000, elk met verschillende ideeën over hardware, firmware en software (d.w.z. slicers ). Het aantal RepRap-ontwerpvarianten steeg enorm, net als hun kwaliteit. Veel van de eerste vrijwilligers richtten organisaties op, waaronder Prusa Research , MakerBot , UltiMaker , LulzBot , E3D , Marlin en meer. Ondertussen komen RepRap-gebruikersgroepen over de hele wereld bijeen en blijven ze de toekomst van 3D-printen vormgeven.
De resultaten
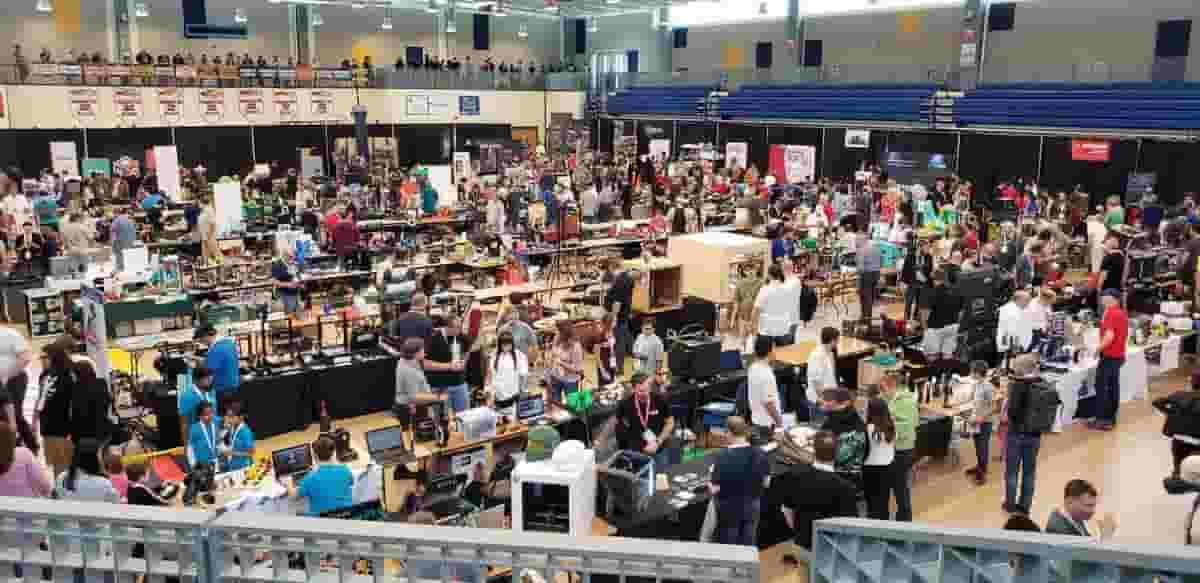
Hoewel RepRap zich voornamelijk richt op toegankelijke fused deposition modeling (FDM) -technologie, heeft het domein van RepRap zich uitgebreid naar vrijwel elke vorm van additieve productie en elke industrie aangeraakt, van geneeskunde tot ruimtevaart . Deze technologie toegankelijk maken voor het grote publiek was op zichzelf al een enorme prestatie, en het was op dit moment dat velen van ons zich begonnen af te vragen of het ooit mogelijk zou zijn om een complete 3D-printer te printen met al zijn componenten.
Hoewel de open-source aard van het ontwerp grote prestaties leverde om het project populairder te maken, zouden de beperkingen van een volledig zelfreplicerend model steeds duidelijker worden naarmate de jaren verstreken. Hoewel talloze nieuwe printerontwerpen werden geïnspireerd door RepRap, werden ze op een gegeven moment allemaal geconfronteerd met de noodzaak om onderdelen en componenten te gebruiken die waren gemaakt door traditionele productie- en assemblageprocessen.
Hoewel veel onderdelen van FDM 3D-printers in verschillende soorten plastic (of kunststofcomposieten) kunnen worden gemaakt, is dat niet alles wat er is met de machines zelf. Van de verwarmingselementen in de extruder tot de technologische apparaten die nodig zijn om de G-code-instructies toe te passen, zijn er componenten nodig die gewoonweg niet in 3D kunnen worden geprint. Om een 3D-printer volledig in 3D te kunnen printen, zou de hardware moeten evolueren om andere materialen te kunnen verwerken.
Het denken achter de vele innovaties blijft evolueren en Dr. Bowyer blijft nieuwe ideeën in de publieke opinie injecteren, waaronder bijvoorbeeld het idee van een “single-shot” elektrische 3D-printer (beschreven in een interview met Thomas Sanladerer ), die 3D-printen in de toekomst een andere richting zou kunnen inslaan.
Krrsantan Bust , Free 3d Model STL.
Elevate Dioramas with Premium 3D Print Models STL Downloads for Resin Printers. Download 3D model STL voor harsprinter – diorama van…
Deluxe Sheep Skull , Free 3d Model STL.
Elevate Dioramas with Premium 3D Print Models STL Downloads for Resin Printers. Download 3D model STL voor harsprinter – diorama van…
Thorin Oakenshield , Free 3d Model STL.
Elevate Dioramas with Premium 3D Print Models STL Downloads for Resin Printers. Download 3D model STL voor harsprinter – diorama van…
TK and Patamon – Digimon , Free 3d Model STL.
Elevate Dioramas with Premium 3D Print Models STL Downloads for Resin Printers. Download 3D model STL voor harsprinter – diorama van…
Tatsumaki , Free 3d Model STL.
Elevate Dioramas with Premium 3D Print Models STL Downloads for Resin Printers. Download 3D model STL voor harsprinter – diorama van…
Xmas Lily cow, Free 3d Model STL.
Elevate Dioramas with Premium 3D Print Models STL Downloads for Resin Printers. Download 3D model STL voor harsprinter – diorama van…